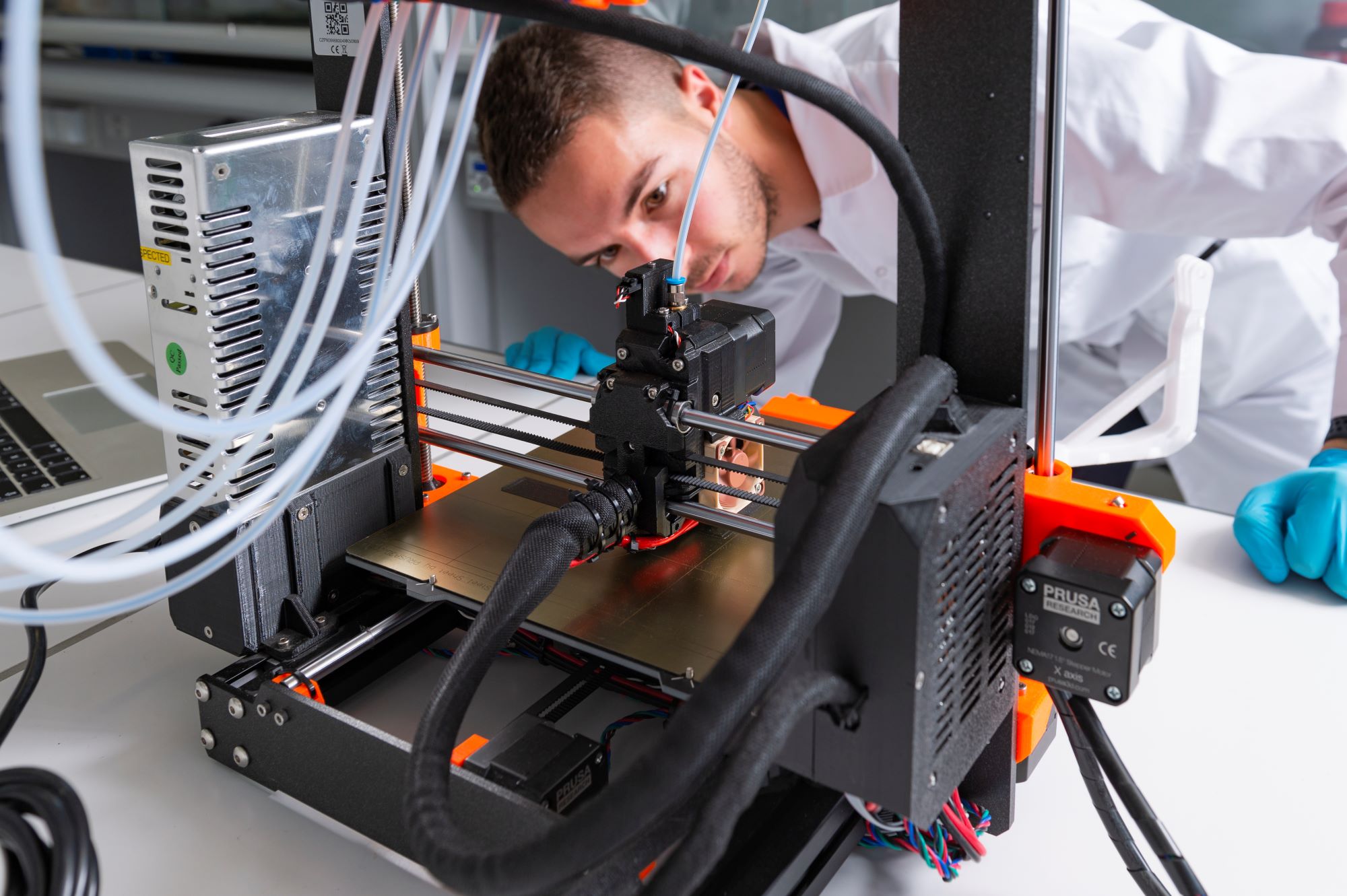
Le grand enjeu
de la transition énergétique
Composante essentielle des véhicules électriques, la batterie lithium-ion est une technologie centrale de la décarbonation de nos moyens de transport. Pour faire face aux problématiques d’approvisionnement des métaux dits « critiques » qui la composent, la valorisation des matériaux présents dans les batteries en fin de vie apparaît comme une solution idéale. Une solution explorée au sein de l’axe Batteries du PEPR, le projet ‘Lulabat’, qui vise à améliorer leurs procédés de recyclage.
Chronique par les membres du projet Lulabat
La demande vertigineuse en batteries lithium-ion impose des besoins historiques pour bon nombre de matières (cobalt, lithium, graphite, etc.), considérées comme « critiques » par l’Union Européenne (UE). Dans un contexte géopolitique contraint, l’UE s’est munie d’une nouvelle réglementation, qui encourage la transition d’une économie linéaire vers une économie circulaire, comme en témoigne le principe de la responsabilité élargie du producteur. Le recyclage de ces objets est une nécessité sociétale et un enjeu de souveraineté pour l’accès aux matières et le développement d’une mobilité décarbonée.
Les procédés de recyclage des batteries au lithium existent et sont notamment industrialisés depuis quelques années en Chine pour le recyclage des batteries lithium-ion des véhicules électriques. L’Europe cherche à devenir indépendante vis-à-vis de la Chine en produisant ses propres batteries lithium-ion et en les recyclant. Cela ne sera possible que si les procédés de production et de recyclage des batteries sont efficients, peu impactant pour l’environnement, et économiquement viables. Il est donc nécessaire d’améliorer les procédés existants pour qu’ils répondent à ces objectifs. La recherche de nouvelles briques technologiques à intégrer dans ces procédés de recyclage est donc essentielle. Le projet Lulabat vise à contribuer à cela en apportant de nouvelles connaissances susceptibles de se transformer en innovations technologiques.
Des procédés actuels inefficients
Les premiers procédés de recyclage des batteries lithium-ion reposaient sur des opérations pyrométallurgiques, consistant à traiter les batteries à haute température (> 1000 °C) afin de récupérer certains métaux, principalement le cobalt, le nickel et le cuivre, tandis que l’aluminium ou le lithium étaient perdus dans les scories, et le graphite, transformé en CO2. Ces procédés présentent une consommation énergétique élevée, une faible capacité à récupérer les métaux sous la forme requise pour leur réutilisation dans la production de nouvelles batteries, et entraînent une perte totale du lithium.
Afin de produire des matériaux compatibles avec la production de batteries, de mieux gérer les impuretés, de réduire les impacts énergétiques et environnementaux, la pyrométallurgie doit être substituée par des procédés de recyclage combinant un traitement mécanique et hydrométallurgique :
Le traitement mécanique des batteries lithium-ion permet de produire un concentré qui pourra être traité par hydrométallurgie, en valorisant l’ensemble des matières.
Les procédés hydrométallurgiques reposent sur l’utilisation d’agents de lixiviation (souvent des solutions acides) pour dissoudre les métaux contenus dans les matériaux des batteries usagées, puis d’opérations chimiques d’extraction, de purification et de séparation, afin de produire différents sels réutilisables pour fabriquer de nouveaux matériaux pour la production des batteries lithium-ion (électrodes, sels de l’électrolyte).
Réduire le coût opératoire de tels procédés consiste notamment à diminuer le nombre d’opérations unitaires et à minimiser les effluents, tout en réduisant la consommation de réactifs et d’énergie. D’autres stratégies sont également envisageables, basées plus particulièrement sur la science des matériaux pour régénérer la fonctionnalité des matériaux des électrodes sans avoir recours à l’hydrométallurgie.
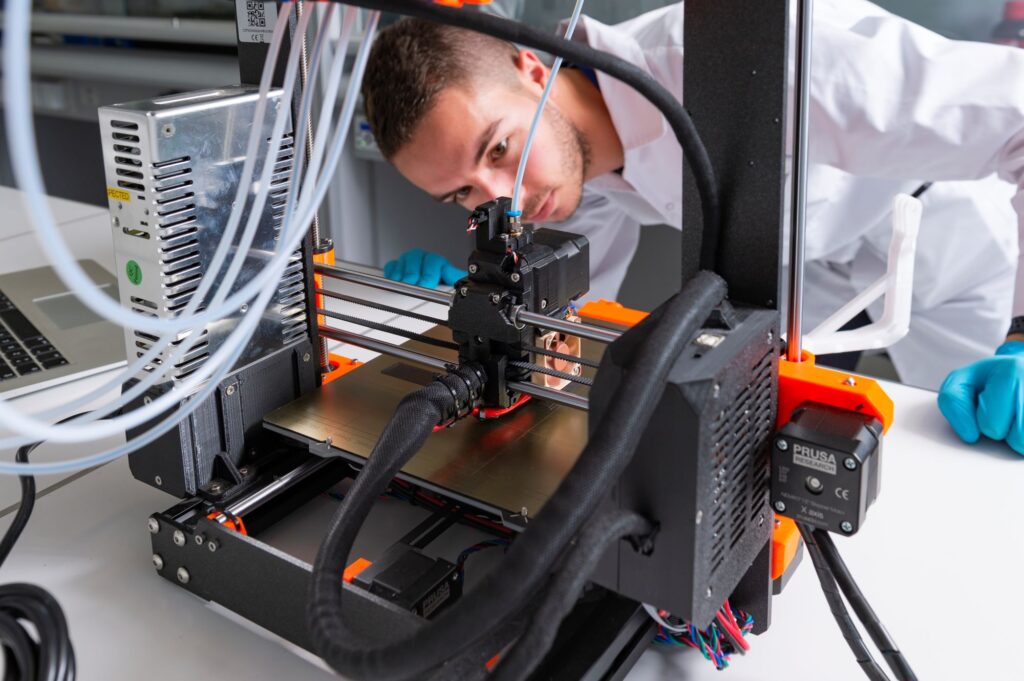
Une croissance sans précédente
Les batteries lithium-ion jouent un rôle central dans le stockage de l’énergie, notamment issue d’une production intermittente (soleil, vent…), mais aussi dans la mobilité électrique, deux enjeux majeurs de la transition énergétique
D’ici à 2030, selon les scénarii, la demande mondiale en batteries lithium-ion devrait atteindre les 2-3 TWh dans le monde, dont 80-90% dédiés aux véhicules électriques (avec près d’un tiers en Europe), soit une augmentation de 30% chaque année. Sur la même période la quantité de déchets devrait connaître une multiplication par 10, qui se répercutera sur la filière de recyclage qui devra évoluer en conséquence.
Les recherches de l’axe Batteries
La première phase du programme de recherche LULABAT se concentre notamment sur le développement de briques technologiques originales et l’estimation de leur intégration dans un procédé hydrométallurgique. Ces briques technologiques illustrées dans la Figure 1 sont :
- La lixiviation par attrition
La première brique concerne l’étape de dissolution (ou lixiviation) de la poudre de batteries usagées. La matière à dissoudre, appelée black mass (BM), est préparée par des étapes de prétraitement physique (broyage, pyrolyse, séparation de l’anode, etc.). L’option technologique étudiée pour la lixiviation des métaux contenus dans la BM est celle de l’attrition-lixiviante. L’intérêt de ce procédé est de rafraîchir l’état de surface des particules par élimination continue des dépôts de surface susceptibles de ralentir ou bloquer leur lixiviation, grâce à la mise en suspension d’un media solide (typiquement des billes de silice de taille millimétrique) dans le réacteur de lixiviation. Dans cet environnement réactif complexe, l’étude porte sur l’exploration des conditions opératoires nécessaires pour une dissolution sélective de certains éléments des BM, en particulier le lithium.
- L’électrodialyse
L’électrodialyse, bien que peu utilisée dans les procédés hydrométallurgiques actuels, est une opération industrielle mature qui permet une séparation efficace des ions avec une consommation réduite de réactifs comparée aux méthodes traditionnelles d’extraction et de séparation. Dans cette partie du programme LULABAT, nous évaluons le potentiel de cette technologie pour le recyclage des batteries lithium-ion. Nous recherchons les conditions optimales pour intégrer l’électrodialyse dès la première étape du procédé, c’est-à-dire après la lixiviation. L’objectif est d’utiliser l’électrodialyse pour l’extraction sélective du lithium, afin de produire de l’hydroxyde de lithium de qualité dite « batterie ». Parallèlement, nous envisageons l’intégration d’autres opérations unitaires en aval de l’électrodialyse, telles que la précipitation, la cristallisation et l’extraction liquide-liquide, pour valoriser les autres métaux présents dans les batteries sous forme de sulfate, tout en réduisant la consommation de réactifs et la production d’effluents.
- La précipitation oxydante
Il s’agit d’une approche chimique qui vise l’extraction des métaux d’intérêt en complément ou substitution des méthodes actuelles. La précipitation oxydante présente des avantages vis-à-vis de la simplicité d’implémentation industrielle, mais aussi de sa complémentarité à l’extraction par solvant pour réduire le nombre d’étages d’extraction. La séparation est réalisable en absence de chlorure et sa capacité est démontrée dans les procédés d’oxydation avancée. Dans le cadre du programme LULABAT, le travail de R&D vise à comprendre les chemins de réactions et les mécanismes mis en jeu en fonction des paramètres de traitement, lesquels conditionnent l’efficacité et la sélectivité de la séparation. Ce travail doit permettre d’identifier des conditions opératoires optimales pour l’évaluation de l’intégration de la technologie dans les procédés de recyclage et la valorisation des métaux critiques.
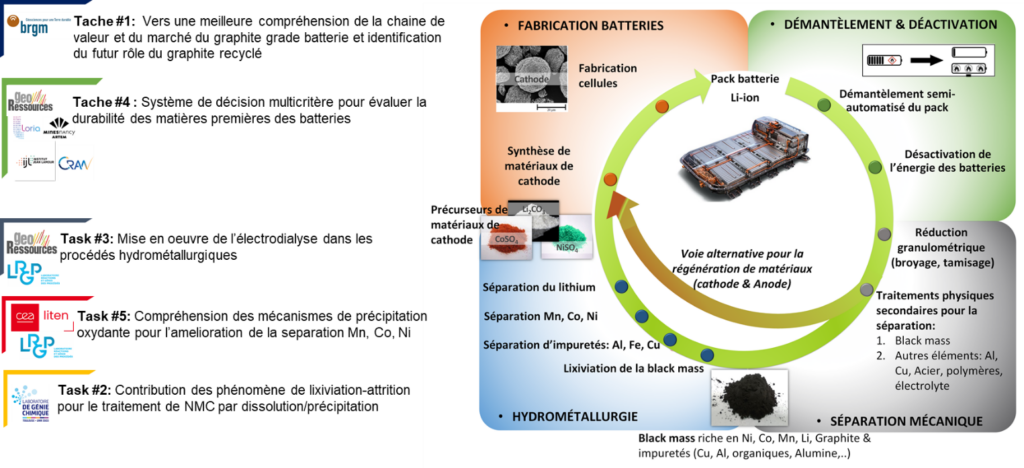
les tâches interviennent principalement dans le processus hydrométallurgique
Plus d'actualités
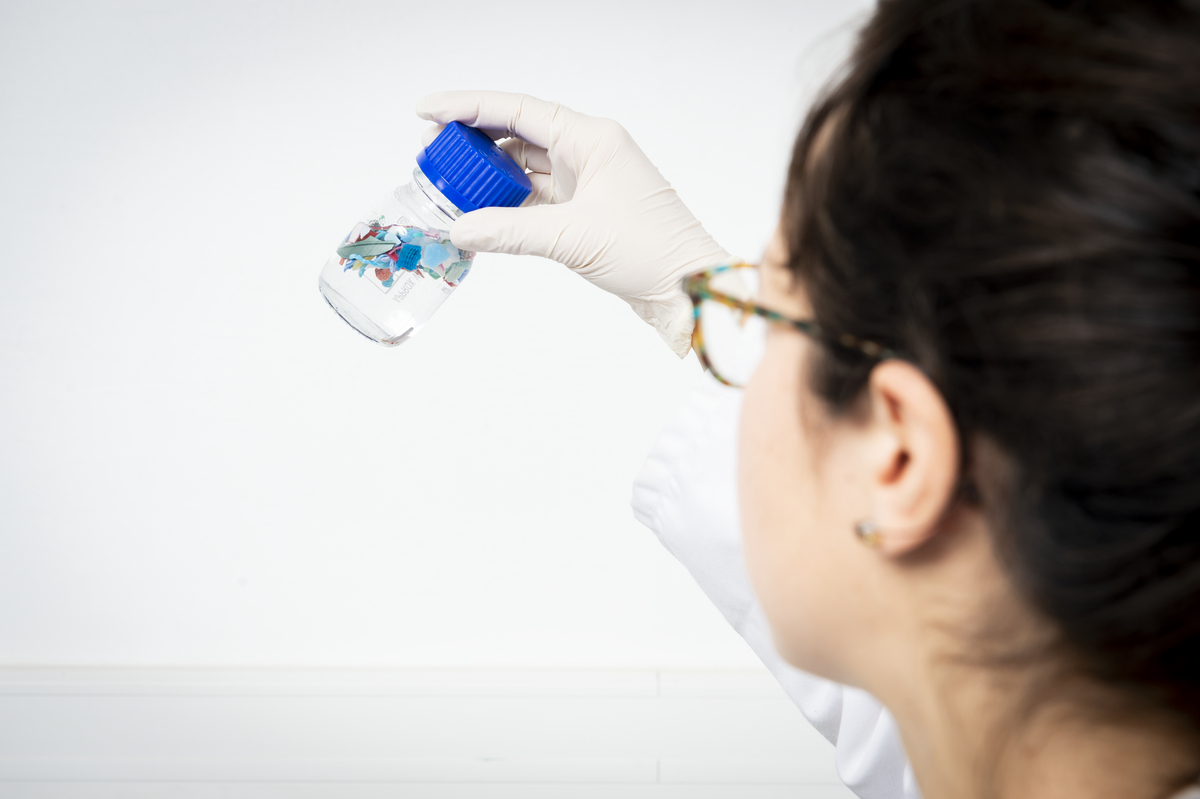
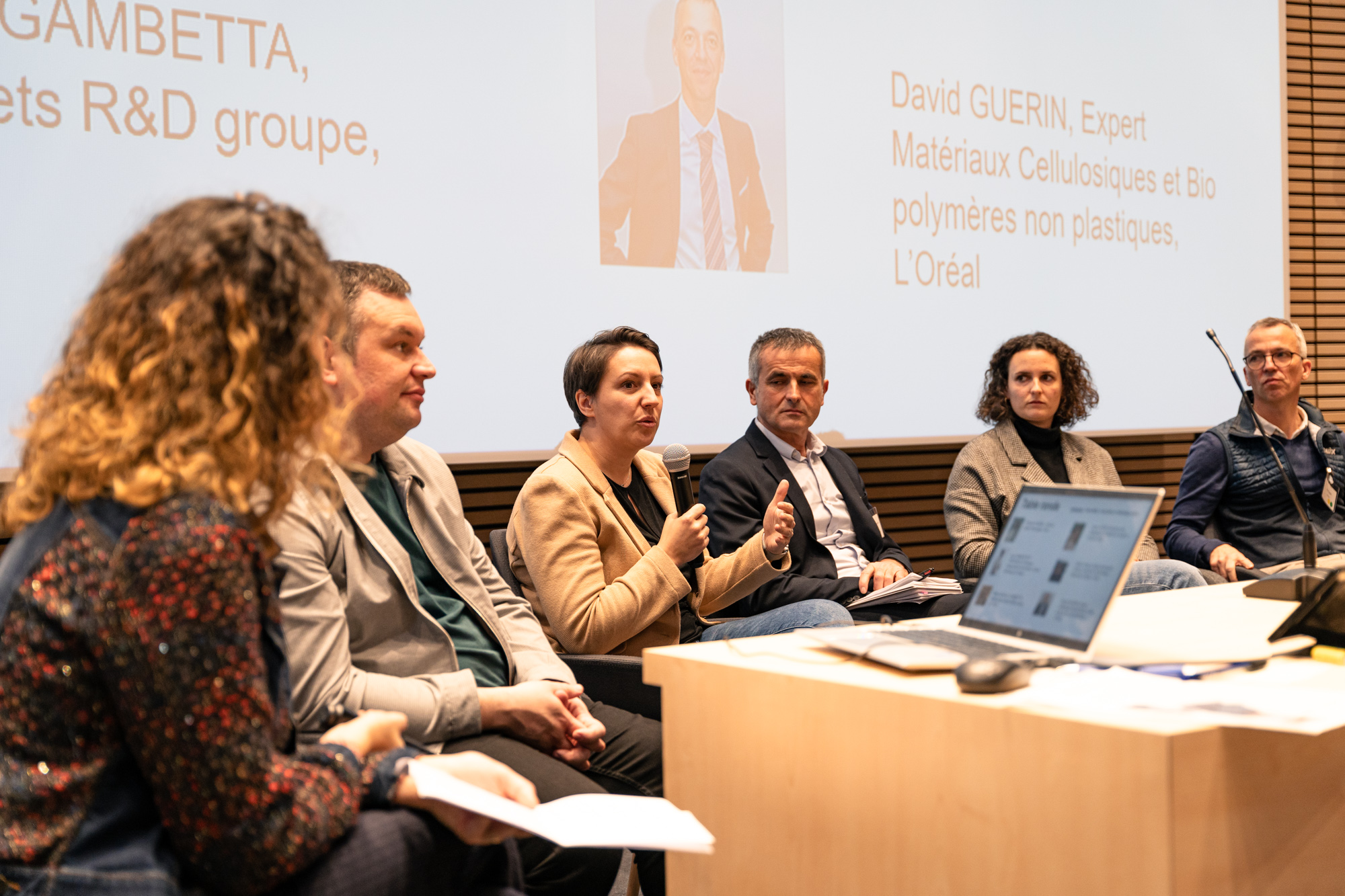
